Data Historian & CIP Reporting
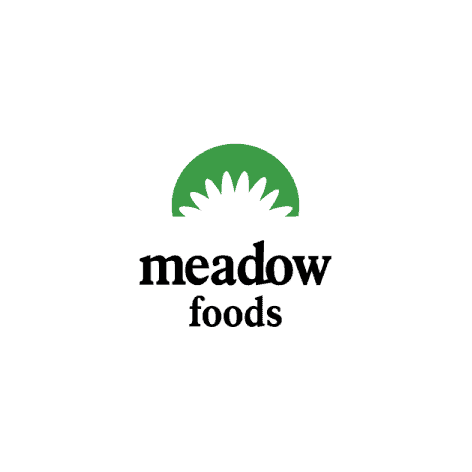
Meadow Foods is the UK’s largest independent dairy and a leading supplier of milk and dairy ingredients to the food industry. Their products are categorised into Butters, Creams, Milks, and Cultured & Sweetened products. These are manufactured in three BRC 6, Grade A, accredited factories and packed into a wide variety of pack sizes to suit their customer’s needs. These factories are utilised to supply over 100,000 tonnes of bulk dairy products to their customers.
The Challenge
In order to cope with around the clock production and to help drive continuous process improvement across their production operations, the company required greater visibility of plant data. Following consultation with Opensoft Systems Ltd, it was agreed to deploy a Data Historian to efficiently collect and store real time data, in order to drive proces
improvements through greater understanding of plant data. The historian allows the business to monitor key metrics relating to process operations throughout the plant.
The Process
Opensoft Systems were chosen to implement the new historian owing to their wealth of experience in integrating automation software across fast-moving process operations. Opensoft recommended a data historian, lending itself well to the real-time process analysis required by the site. The system linked seamlessly to the site’s Kepserver I/O server providing a real-time data stream across the plant’s Mitsubishi Q Series PLCs.
CIP (clean in place) is an important requirement for any food production facility, a change in products manufactured requires a thorough clean of all process equipment prior to re-utilisation for new recipes. Process values such as clean type, temperature, and pressure must be captured by the system for each clean which acts as proof of traceability for end customers and regulatory bodies.
The Result
Following system implementation, training was provided to assist personnel in understanding the configuration of the historian server’s utilities, management of the system, data analysis and production of reports. The software allows for information to be reported in a variety of ways from trends to tabularised data allowing data to be exported to Excel for further analysis.
Client's Feedback
“Opensoft Systems were chosen to implement the new historian owing to their wealth of experience in integrating automation software across fast-moving process operations.
The system linked seamlessly to the sites Kepserver I/O server providing a real-time data stream across the plants Mitsubishi Q Series PLCs.
Following system implementation, training was provided to assist personnel in understanding the configuration of the historian server’s utilities, management of the system, data analysis and production of reports.
‘Meadow Foods’ Group Engineering Manager commented:
We needed a tool that allowed us to understand after-the-event issues across our plant. Opensoft installed the historian with minimal fuss and aligned the reports to our needs very well.”
Engineering Manager
Meadow Foods